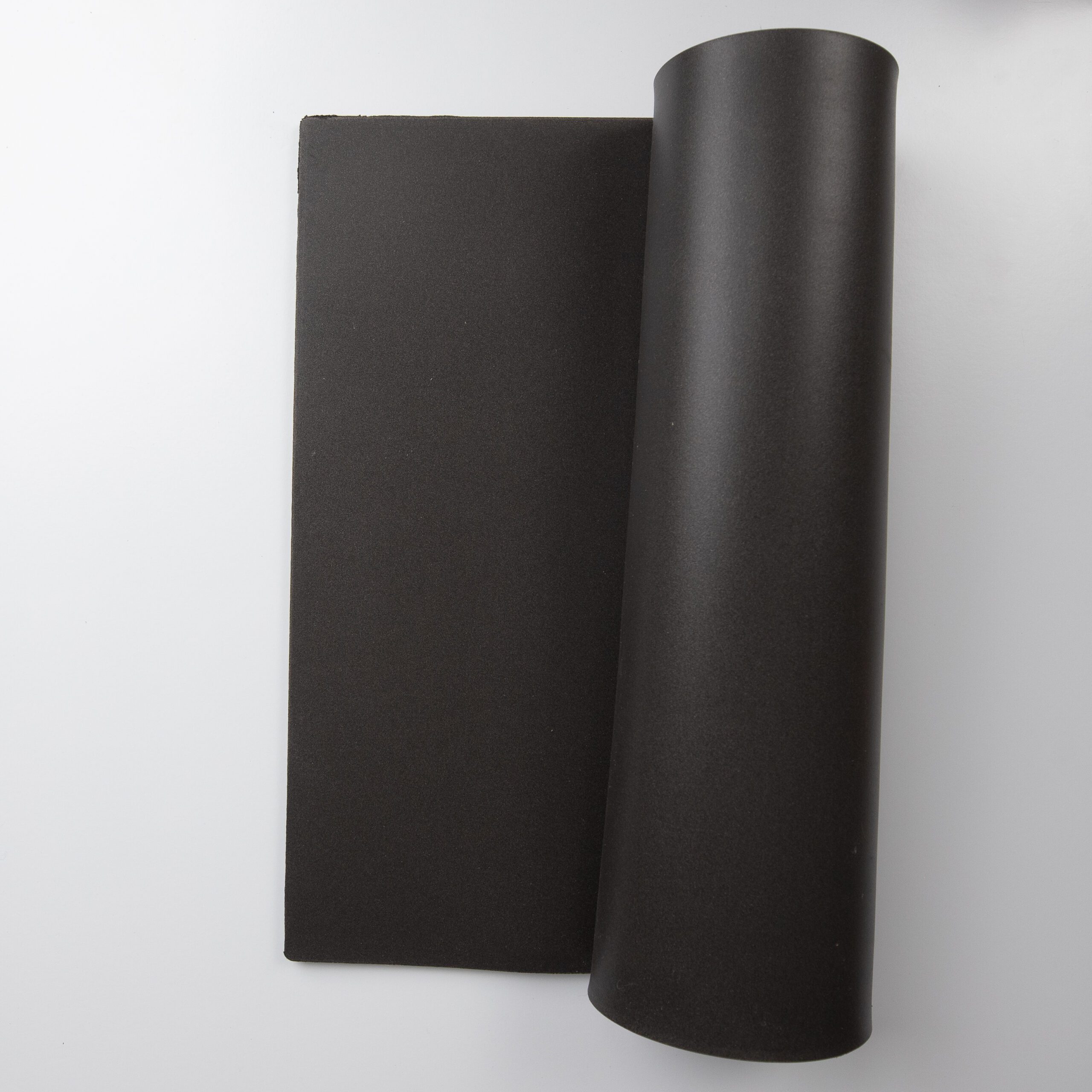
SSP2529
SSP2529 is a 68-durometer, nickel-aluminum EMI shielding silicone. Resists galvanic corrosion. MIL-DTL-83528 tested. Use instead of CHOSEAL 6502.
SSP makes nickel-aluminum silicones and flurorosilicones designed for corrosive environments with heavy salt spray, including military ships and marine applications.
Choose sheets, rolls, moldable compounds, extrusions, EMI O-rings, or EMI gaskets.
SSP’s corrosion resistant EMI shielding silicones combine electrical conductivity and EMI shielding with resistance to galvanic corrosion, a problem in marine environments. Our nickel-aluminum-filled elastomers are a cost-effective alternative to silver-filled products and include offsets to CHO-SEAL 6502 and CHO-SEAL 6503 from Parker Chomerics.
SSP2529 is a 68-durometer, nickel-aluminum EMI shielding silicone. Resists galvanic corrosion. MIL-DTL-83528 tested. Use instead of CHOSEAL 6502.
SSP2551 is a 72-durometer nickel-aluminum flluorosilicone. Tested to MIL-DTL-83528 and performs to 40 GHz. Resists fuels, solvents, galvanic corrosion.
EMI/RFI shielding silicones that contain nickel-aluminum particles provide reliable protection against salt spray, salt water, and atmospheric humidity. Resistance against galvanic protection is especially important in marine applications, but engineers and material buyers must also account for supplier performance.
Typically, EMI gaskets are installed between flanges that contain different metals than the gasket itself. Most flanges are made of aluminum or steel, but many EMI gaskets contain silver, nickel, Monel, or other metals. EMI gaskets are electrically conductive, too.
In environments with salt spray, salt water, or atmospheric humidity, fluids collect at the flange-gasket interface. This provides the electrolyte that’s needed for galvanic corrosion. In this galvanic cell, a loss of material occurs with the most noble, or least corrosion-resistant, metal.
To avoid galvanic pitting, some metal flanges are treated with anti-corrosion coatings that also provide electrical conductivity. For example, aluminum flanges in marine or aerospace applications may be treated with a chromate conversion coating such as Iridite. These specialized finishes help, but engineers and buyers still need the right EMI silicones to minimize corrosion-related repairs.
Galvanic corrosion is the most common corrosion-related condition to affect EMI gaskets. Known as “dissimilar metal corrosion”, this electrochemical process occurs when:
SSP also offers these other types of EMII/RFI shielding materials. We also fabricate EMI gaskets and EMI O-rings from the elastomers we make.