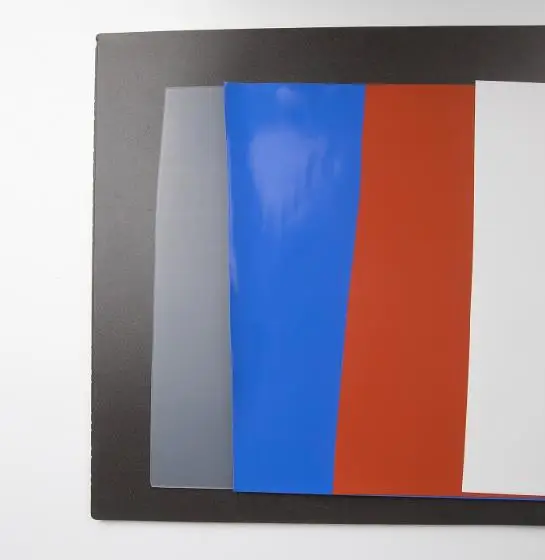
SSP122
SSP122 is a 60-durometer, peroxide-catalyzed, heat-cured silicone elastomer that meets the requirements of A-A-59588, Class IA and 1B, Grade 60. Find out if this silicone rubber is right for your application.
SSP makes A-A-59588 silicones and supplies them as sheets, rolls, and ready-to-mold compounds.
This aerospace spec is sometimes written as MIL SPEC AA-59588, AA 59588, AA59588, or A A 59588 instead.
AA-59588 replaces ZZ-R-75, which is still used on some part drawings.
Use the tables below to find A-A-59588 silicones from SSP. You’ll also find more information about the A A 59588 spec and its classes and grades.
A-A-59588 is a U.S. General Service Administration (GSA) specification that supersedes ZZ R 765. Sometimes, these standards are written as AA-59588 or AA 59588, or as ZZ-R-765 or ZZ-R-765/GEN. ZZ R 765 still appears on some prints, but it’s an older standard referenced by National Stock Number (NSN) 5330-01-371-7183 to ensure standardization among military buyers in NATO countries.
AA 59588 divides aircraft silicones and aviation silicones into six classes, each with durometer-based grades on the Shore A scale. These spec-grade materials are valued for their resistance to high temperatures, low temperatures, tear, and flex fatigue.
The table below provides an overview of AA 59588 silicones. Applications include aircraft parts like engine mounts, vibration-isolating mounts, and exhaust hangers.
Class | Description | Grades |
1A | Low temperature resistant | 40, 50, 60, 70, 80 |
1B | Low temperature resistant and low compression set at high temperature | |
2A | High temperature resistant | 40, 50, 60, 70, 80 |
2B | High temperance resistant and low compression set | 40, 50, 60, 70, 80 |
3A | Low temperature, tear and flex resistant | 30, 50, 60 |
3B | Tear and flex resistant | 30, 50, 60, 70, 80 |
The A-A-59588 specification replaced ZZ-R-765E (ZZ-R-765, ZZ-R-765/GEN. ZZ R 765E).
Specification | Alternative Spellings | Descriptions |
A-A-59588 | AA-59588 | See tables above |
ZZ-R-765 | ZZR765, | Class 1 Extreme low temperature phenyl base silicone |
ZZ-R-765 | ZZR765, | Class 2 General purpose, low compression set methyl-vinyl silicone |
ZZ-R-765 | ZZR765, | Class 3 High flex, high tear strength grades of methyl-vinyl silicone |
These A-A-59588 silicones meet the requirements of Class 1A or Class 1B are intended for use where resistance to extremely low temperatures is required. The A-A-59588 specification defines this as approximately -73°C (-100°F).
Class 1 materials can also resist extreme high temperatures of approximately 210°C (425°F); however, their length of service at high temperatures is less than that of Class 2 materials. Note that Class 1B silicones have low compression set at high temperatures.
SSP122 is a 60-durometer, peroxide-catalyzed, heat-cured silicone elastomer that meets the requirements of A-A-59588, Class IA and 1B, Grade 60. Find out if this silicone rubber is right for your application.
SSP227 is a 50-durometer, peroxide-catalyzed, heat-cured silicone elastomer that meets the requirements of A-A-59588, Class IA and Class 1B, Grade 50. Find out if this silicone rubber is right for your application.
SSP266 is a 70-durometer, peroxide-catalyzed, heat-cured silicone elastomer that meets the requirements of A-A-59588, Class IA and Class 1B, Grade 70. Find out if this silicone rubber is right for your application.
SSP278 is a 40-durometer, peroxide-catalyzed, heat-cured silicone elastomer that meets the requirements of A-A-59588, Class IA and Class 1B, Grade 40. Find out if this silicone rubber is right for your application.
These AA 59588 meet the requirements of Class 2A or Class 2B resist extreme high temperatures of approximately 219°C (425°F). They also have low temperature resistance, but only to about -62°C (-80°F). Unlike like Class 2A materials, however, Class 2B silicones have low compression set. In other words, they have high resilience.
SSP220 is a 40-durometer, peroxide-catalyzed, heat-cured silicone elastomer that meets the requirements of A-A-59588, Class 2A and Class 2B, Grade 40. Find out if this silicone rubber is right for your application.
SSP301 is a 50-durometer, peroxide-catalyzed, heat-cured silicone elastomer that meets the requirements of A-A-59588, Class 2A and Class 2B, Grade 50. Find out if this silicone rubber is right for your application.
SSP352 is a 60-durometer silicone that meets AMS 3303 and AA 59588 Class 2A and 2B, Grade 60. It’s supplied in different form factors and colors.
SSP389 is a 70-durometer, peroxide-catalyzed, heat-cured silicone elastomer that meets the requirements of A-A-59588, Class 2A and Class 2B, Grade 70. Find out if this silicone rubber is right for your application.
SSP390 is a 25-durometer, peroxide-catalyzed, heat-cured silicone elastomer that meets the requirements of A-A-59588, Class 2A and Class 2B, Grade 25. Find out if this silicone rubber is right for your application.
SSP391 is an 80-durometer, peroxide-catalyzed, heat-cured silicone elastomer that meets the requirements of A-A-59588, Class 2A and Class 2B, Grade 80. Find out if this silicone rubber is right for your application.
AA 59588 Class 3A silicones provide resistance to extremely low temperatures of approximately -75°C (-103°F). Importantly, these military and aerospace silicones also resist tearing and flexing. AA59588 Class 3A silicones also resist extreme high temperature environments to approximately 204°C (400°F). Applications include engine mounts and exhaust hangars.
A-A-59588 Class 3B silicones also resist tearing and flexing, but their resistance to extreme low temperature is less than that of Class 3A materials. With A-A-59588 silicones that meet the requirements of Class 3B, the temperature range is approximately between -70°C (-95°F) and 204°C (400°F). Applications include aircraft door seals, window seals, and vibration mounts.
SSP200-T, military silicones, aerospace silicones, automotive silicones, fatigue testing, flex-fatigue resistance, demattia flex resistance text, a-a 59588 Class B Grade 50
SSP2521-T is a 70-durometer silicone that meets all A-A-59588, Class 3B, Grade 70 requirements and passes the DeMattia Flex Resistance Test.
SSP2523-T is a 50-durometer, low-temperature, high tear strength, heat-cured silicone with flex resistance that meets A-A-59588, Class 3A, Grade 50.
SSP392-T is a 60-durometer silicone that meets all A-A-59588, Class 3B, Grade 60 requirements and passes the DeMattia Flex Resistance Test.
Flex, or flexural fatigue, is cracking caused by cyclical stresses and strains. Small cracks propagate into larger cracks that, ultimately, can result in failure. Fully-compliant materials must pass the DeMattia Flex Resistance test, which measures crack growth in inches over thousands of flexural cycles.
Some suppliers claim that their silicones are flex-fatigue resistant, but industry-wide compliance has been inconsistent. Other suppliers say that their products meet the A-A-59588 3B standard, but their elastomers are not certified to meet the flexural requirements of 3B.
Specialty Silicone Products (SSP) supplies aerospace and military silicones that have been independently-tested and certified to the flexural requirements of A-A-59588, Class 3B for several grades. To our knowledge, SSP is the only manufacturer that certifies materials to this specification with a third-party verification and no exceptions for flex-testing.
SSP will flex-test competitive products at no charge, and encourages sourcing managers and product engineers to choose compounds that pass the DeMattia Flexural Test.
Fully-compliant A-A-59588, Class 3B silicones must pass the DeMattia Flex Resistance Test, a dynamic test that measures crack growth in inches over thousands of flexural cycles. The ASTM D813 – 07(2014) Standard Test Method for Rubber Deterioration–Crack Growth defines this testing protocol.
The DeMattia Flexural Test is one of several fatigue tests, but it’s a critical one for demanding applications. For example, aerospace engineers need silicones with high flex-fatigue resistance for door seals, window seals, and vibration-isolating mounts used with alternators, compressors, and assembly bolts.
SSP supplies silicones with high flex-fatigue resistance, a measure of a material’s ability to withstand repeated flexing or bending without cracking. These silicones pass the DeMattia Flex Resistance Test and meet the full requirements of the A-A-59588 3B specification – with no exceptions for flexural testing.
Use the table below to compare the A-A-59588 military and aerospace silicones that SSP makes.
Elastomer | A-A-59588 Callouts | Product Specifications | |||
Product No. | Class | Grade | Durometer (Shore A) | Tensile Strength (psi) | Elongation (%) |
3A | 50 | 50 | 1493 | 807 | |
3B | 50 | 50 | 1280 | 660 | |
3B | 60 | 60 | 1280 | 650 | |
3B | 70 | 70 | 1238 | 462 | |
2A, 2B | 25 | 10 – 80 | 870 – 1475 | 700 – 1200 | |
2A, 2B | 40 | 40 | N/A | N/A | |
2A, 2B | 50 | 50 | 1100 | 450 | |
2A, 2B | 60 | 60 | 1000 | 300 | |
2A, 2B | 70 | 70 | 1000 | 250 | |
2A, 2B | 80 | 80 | 1200 | 150 | |
1A, 1B | 40 | 40 | 1000 | 500 | |
1A, 1B | 50 | 50 | 1300 | 500 | |
1A, 1B | 60 | 60 | 1100 | 500 | |
1A, 1B | 70 | 70 | 1100 | 450 |
SSP makes A-A-59588 silicones and supplies them as sheets, rolls, and ready-to-mold compounds.